Crafting gun parts with precision and accuracy is a skill. It requires the right tools and knowledge.
In today's manufacturing industry, Computer Numerical Control (CNC) machines have revolutionized the way gun parts are made. These machines can precisely cut and shape metal, making custom gun parts easy to create.
In this article, we will explore the process of making gun parts with a CNC machine. We will also look at the steps involved in achieving the perfect fit and finish for any firearm.
What You Need to Know Before Making Gun Parts with a CNC Machine
Understand the Gun Control Act
Under the Gun Control Act, individuals need to understand the rules when making gun parts with a CNC machine. This involves knowing how the act affects making and distributing gun parts with CNC machines. Legal requirements and restrictions in the Gun Control Act, such as getting the right licenses, keeping records, and following rules for selling and transferring firearms, are important to follow. Not following these rules can lead to fines and criminal charges.
It's very important for people making gun parts with CNC machines to fully understand and follow the Gun Control Act.
CNC Machine Basics for Beginners
Working with CNC machines, especially for beginners, requires following basic safety rules to prevent accidents and ensure smooth operation. Beginners should always wear proper safety gear, such as eye and hearing protection, and avoid loose clothing or jewelry that could get caught in the machine. It's important to securely clamp workpieces and carefully select cutting tools and work holding fixtures when setting up the machine.
For making gun parts with a CNC machine, beginners should also calibrate the machine, program cutting paths, and maintain the correct feed rates and spindle speeds for different materials. Regularly inspecting and replacing cutting tools is essential to ensure precision and avoid tool breakage. Understanding how to troubleshoot common problems, like tool chatter or poor surface finish, is also important.
Safety Rules for Working with CNC Machines
Operators who work with CNC machines should follow essential safety rules for a secure environment. Always wear safety glasses and gloves when using the machinery to prevent harm. Keep the work area clear and secure the CNC machine to the floor to prevent movement during operation. Operators need proper training and must follow safety protocols. Regular maintenance and inspections are also important to prevent accidents and injuries.
These precautions ensure safety when working with CNC machines, especially in manufacturing gun parts.
Choosing the Right CNC Machine for Making Gun Parts
Overview of SYIL Machine Tools
SYIL Machine Tools offer features and capabilities ideal for precision manufacturing. The SYIL X7 model is designed for gunsmithing, with a work envelope of 10" x 12" (X,Z), a spindle speed of 3,500 RPM, and a 3 hp motor. These specs are essential for high accuracy and precision in making gun parts. The Single-phase 230 Vac power supply and financing options through Geneva Capital make the SYIL X7 model practical for gunsmithing workshops.
Other SYIL CNC machines, like the SYIL X5 and the SYIL X4, also have similar capabilities and work envelope sizes, making them versatile options for various gunsmithing needs.
SYIL X7 for Gunsmithing
The SYIL X7 CNC machine is powerful and efficient. It has 3 horsepower and a spindle speed of 3,500 RPM. This makes it suitable for gunsmithing. It runs on a single-phase 230 Vac power source and has a work envelope of 10" x 12" (X,Z). This provides the necessary capacity for creating various gun parts with precision. The machine's financing options also make it accessible to gunsmiths. Compared to other CNC machines, the SYIL X7 stands out for its precision and reliability.
This ensures that gun parts are manufactured with accuracy and consistency. Safety protocols are important for operating the SYIL X7 safely. This includes wearing appropriate personal protective equipment and following machine operating instructions.
Additionally, regular maintenance and inspections should be conducted to ensure that the machine functions optimally and safely.
Other Suitable CNC Machines for Gun Parts
When it comes to manufacturing gun parts, there are several CNC machines to consider. These machines include CNC lathes, mills, and routers. Each machine has its own advantages and limitations, serving specific purposes.
CNC lathes are best for making cylindrical gun components like barrels and pins. Mills can create more complex parts like trigger housings or slides. Routers are great for intricate designs or engravings on gun stocks or grips.
Compared to SYIL Machine Tools, these alternative machines offer different work envelopes, spindle speeds, and power outputs that may better suit the specific needs of a gunsmith or manufacturer. Factors to consider when choosing a CNC machine for making gun parts include precision, material, work envelope, spindle speed, and power.
Cost and financing availability might also be important factors to consider in the decision-making process.
Steps in Making Gun Parts with a CNC Machine
Design the Gun Part
When designing gun parts for CNC machining, it's important to consider several factors to ensure success.
First, the design should account for the capabilities of the CNC machine. This includes the spindle speed, power, and work envelope. For example, a spindle speed of 3,500 RPM and a work envelope of 10" x 12" in the X and Z axes will influence the design parameters.
Additionally, careful consideration should be given to the material of the gun part and the cutting tools to align with the capabilities of the CNC machine.
Designers should also focus on the part's geometry to ensure effective machining without interference or alignment issues.
Furthermore, it's crucial to optimize the design for efficient toolpaths to minimize production time and cost.
By following these best practices, gun parts can be effectively designed for CNC machining, resulting in high-quality and precise products.
Set Up the CNC Machine
To make gun parts with a CNC machine, some key things are needed.
The machine should be in a well-lit and ventilated area, and the surrounding should be clean. This makes sure everything works properly.
Safety gear like goggles and gloves should be worn, and the power supply should be turned off before making adjustments. Keeping the work area clear is also important.
When choosing the material for making gun parts, think about its strength and durability for high-speed machining.
The material should be securely held in place using the right tooling and fixturing for accurate cuts.
Consider the size and weight of the material to ensure it fits within the machine's working area and doesn't exceed its load capacity for good performance and safety.
Choose the Right Material
When making gun parts with a CNC machine, selecting the right material is an important decision. You should consider factors like strength, durability, machinability, corrosion resistance, and wear resistance. Materials such as aluminum, stainless steel, and titanium are commonly used due to their ability to handle the forces and pressures involved in gun operation.
The choice of material significantly affects the quality and performance of the gun parts. It should withstand high temperatures and pressures, while also offering stability and precision in machining.
For example, using aluminum for lightweight components and stainless steel for parts requiring strength and corrosion resistance ensures effective firearm performance.
Key considerations for ensuring the chosen material is suitable for machining on a CNC machine include hardness, thermal conductivity, and chip formation during the machining process. Harder materials like titanium require specialized cutting tools and machining parameters to achieve the desired shapes and dimensions without affecting the material's properties. These considerations are important for producing accurate and reliable gun parts.
Secure the Material on the Machine
To keep the material safe on the CNC machine and avoid it moving while being worked on, it's important to use clamps or vises made for this purpose. These tools hold the material firmly in position and stop it from shifting during machining. Using the right fixtures and jigs is also important, especially with irregularly shaped parts. When working with different materials, like metal or plastic, it's important to choose the right clamping or fixturing methods based on the material's properties.
For example, gentle soft jaws can be used for delicate materials like plastic, while tough hard jaws are better for metal parts. This makes sure the material is securely held in place throughout the machining process and results in accurate and precise production of gun parts.
Run the CNC Machine
To set up the CNC machine for making gun parts, the user needs to:
Ensure necessary tooling and workholding devices are in place.
Load cutting tools into the machine's tool carousel.
Input the correct program into the CNC controller, specifying tool paths and cutting parameters.
Once the setup is complete, the user can proceed with:
Activating the machine.
Executing the programmed tool paths.
Closely monitoring the machining process for accuracy and efficiency.
Safety is crucial when operating a CNC machine for gun parts production. Users should:
Wear appropriate personal protective equipment.
Be mindful of moving parts and potential cutting hazards.
Familiarize themselves with emergency stop and other safety features to prevent accidents and injuries.
Making Gun Parts with a CNC Machine: Detailed Guide
Program the Machine for the Specific Gun Part
To program a CNC machine for a specific gun part, the operator needs to input the required codes or commands. These include the design dimensions, tooling information, and cutting speeds. For example, G-code controls the movement of the tool, and M-code handles miscellaneous machine functions.
Setting up the CNC machine's work envelope in accordance with the part's specifications is crucial to ensure precise and accurate machining. This involves adjusting the X and Z axis work envelope parameters based on the size and shape of the gun part.
Furthermore, optimizing the production of the gun part involves specific parameters and adjustments, such as spindle speed and power supply requirements. These may vary based on the material and complexity of the part. These settings can impact the overall efficiency and quality of the manufacturing process, making it imperative to fine-tune the CNC machine for each specific gun part.
Begin the Machining Process
Programming the CNC machine to start making specific gun parts involves entering the exact measurements and specifications into the machine's software.
You need to have a good understanding of G-code and CNC machining tools to make sure the gun part is accurately replicated.
Before starting the machining process, it's important to take safety measures like securing the workpiece, wearing protective gear, and ensuring the machine is working properly to avoid accidents.
To control the quality of the machining process, regularly inspect the tooling, calibrate the machine, and get real-time measurement feedback to ensure the dimensions and surface finishes of the gun parts are within the specified tolerance.
It's also important to regularly maintain and clean the machine to improve its performance and maximize the production of high-quality gun parts.
Monitor the Machining for Quality Control
To ensure the production of quality gun parts with a CNC machine, it's important to closely monitor the machining process. This includes regularly checking the dimensions and surface finish of the parts. It's also crucial to inspect the cutting tools to ensure they're sharp and in good condition.
When monitoring for quality control, watch out for deviations from specified dimensions, rough surface finishes, and tool wear. If any issues arise, immediate steps should be taken to fix the problem. This may involve adjusting cutting parameters, replacing worn-out tools, or recalibrating the machine for accurate production.
By implementing these monitoring and corrective measures, manufacturers can maintain the quality and precision of gun parts made with CNC machining.
Finishing the Gun Parts After CNC Machining
Remove from CNC Machine
Before removing any part from a CNC machine when making gun parts, it's important to ensure that the part is securely held in place. This helps to prevent accidents or material damage from a loose or unstable piece.
It's also very important to follow safety precautions before removing a part from the CNC machine. This includes wearing the right protective gear, like gloves and safety goggles, and making sure the machine is turned off and all moving parts have stopped. Failing to follow these safety measures can lead to serious injury or damage to the CNC machine.
So, it's important to take the time and care needed to properly secure and safely remove the gun parts from the machine.
Clean and Polish the Part
To properly clean and polish a gun part after CNC machining, it is necessary to have a set of cleaning products and tools including a degreaser, a soft brush, and a lint-free cloth. The degreaser is used to remove any oily residue from the part, while the soft brush and cloth are used to gently scrub and dry the part without leaving behind any lint or scratches.
To achieve a smooth and professional finish, the part can be further polished using a fine-grit sandpaper or polishing compound, whichhelps to remove any burrs or imperfections left from the machining process. It is crucial to ensure that the part is free from any debris or defects after cleaning and polishing. This can be done by carefully inspecting the part under bright lighting and using a magnifying glass if necessary. Any remaining debris or defects should be addressed with additional cleaning or polishing until the part meets the desired quality standards set by the manufacturer.
Inspect for Defects
After CNC machining gun parts, it is important to inspect for defects. Any visible defects on the gun parts, like surface imperfections, scratches, or irregularities, could affect the quality and functionality of the parts.
It is important to ensure that all dimensions and features have been carefully inspected for defects, including hole diameters, thread depths, and surface finishes. Any anomalies, no matter how minor, need to be thoroughly addressed to prevent potential issues in the future, establishing the highest quality and safety standard for the gun parts.
This includes a careful examination for any signs of chipping, warping, or unusual discoloration. By conducting a thorough inspection for defects, manufacturers can guarantee the reliability and accuracy of the gun parts produced with the CNC machine, ensuring the highest level of precision and overall quality.
Advanced Tips for Making Gun Parts with a CNC Machine
Select Advanced Tools and Attachments
Choosing the right tools for CNC machining gun parts is important for precision and high-quality results. Factors like spindle speed, power, and work envelope must be considered.
For example, a 3 hp spindle with 3,500 RPM and a work envelope of 10" x 12" can provide the needed power and precision. Using 3D simulations to optimize machining paths is effective. It helps visualize the process, identify issues, and make adjustments before production, reducing errors and ensuring accuracy. Investing in advanced tools and using 3D simulations is essential for optimal results in CNC machining gun parts.
Optimize Machining Paths
Manufacturers can optimize machining paths for gun parts production with a CNC machine. They use advanced software and techniques to analyze and refine toolpaths. By incorporating high-speed machining and adaptive roughing strategies, they improve efficiency and precision.
Additionally, toolpath optimization software reduces production time and material waste. These measures create a more streamlined manufacturing process. This ultimately boosts productivity and cost-effectiveness in gun part production with a CNC machine.
Use 3D Simulations for Better Results
Using 3D simulations can improve the accuracy of making gun parts with a CNC machine. Manufacturers can see the entire machining process digitally before any physical tooling, reducing errors and waste.
Benefits of using 3D simulations in the CNC machining process for gun parts include faster production, fewer mistakes, and identifying issues beforehand. This helps in making adjustments and improvements to the design before manufacturing.
By using 3D simulations, the final products can meet quality standards and specifications, resulting in better outcomes for gun part production with a CNC machine.
Troubleshooting Common Issues in Making Gun Parts with a CNC Machine
Material Slippage during Machining
Material slippage during machining can happen for several reasons. These include using the wrong tool, not setting the right cutting parameters, or having inadequate workholding.
For example, using the incorrect tool can cause excessive vibrations, making the material move during cutting. To prevent this, manufacturers can use suitable cutting tools, optimize cutting speeds, and use effective clamping methods. A stable workholding fixture can help secure the material, reducing the chance of slippage. The consequences of material slippage include inaccurate part dimensions, surface defects, and tool breakage. If the material shifts during machining, it can lead to incorrect dimensions and compromised part quality, resulting in rework or part rejection. Understanding and addressing the causes of material slippage are important for making precise and high-quality gun parts with a CNC machine.
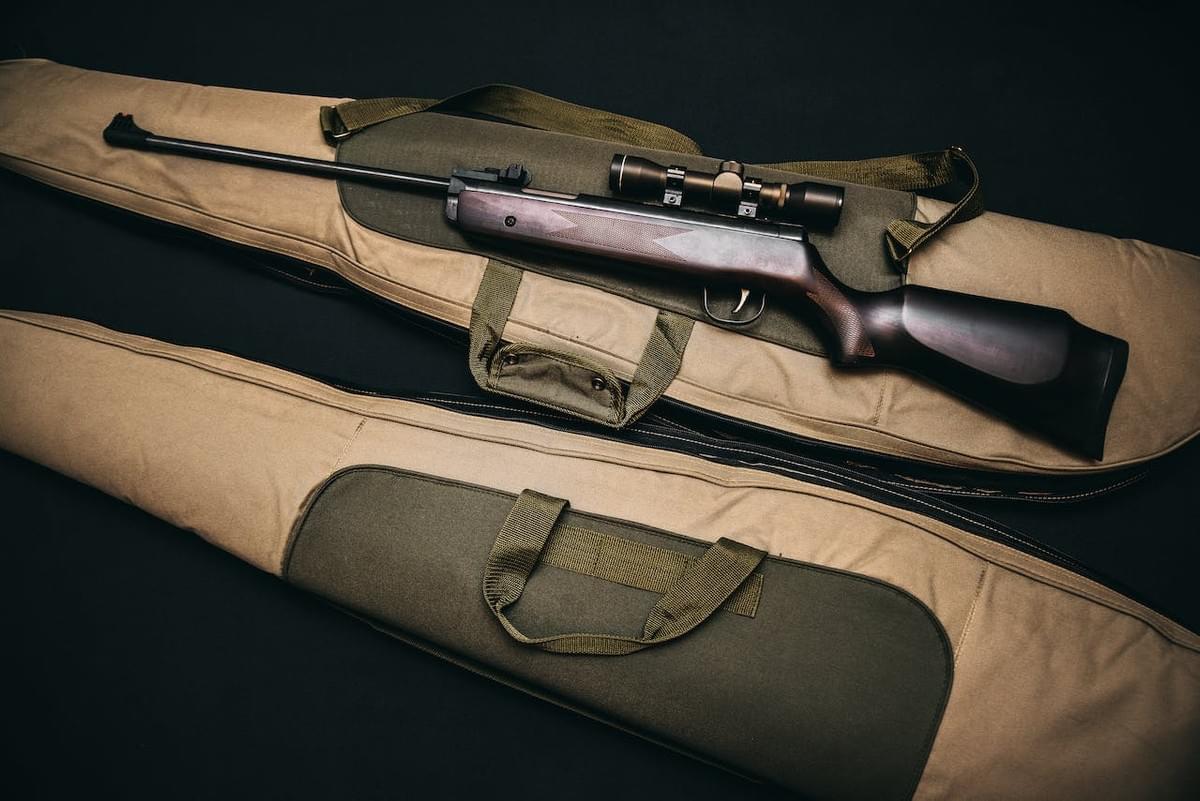
FAQ
What are the necessary skills and knowledge to make gun parts with a CNC machine?
The necessary skills and knowledge to make gun parts with a CNC machine include proficiency in CAD/CAM software, understanding of metalworking and machining processes, knowledge of different types of cutting tools, and experience in operating CNC machines. Familiarity with firearms and their components is also important.
What materials are commonly used for making gun parts with a CNC machine?
Commonly used materials for making gun parts with a CNC machine include steel, aluminum, titanium, and polymer.
What are the safety precautions that need to be taken when making gun parts with a CNC machine?
The safety precautions when making gun parts with a CNC machine include wearing protective gear such as goggles and gloves, securing the workpiece properly, and using proper machining techniques to prevent accidents.
Are there any legal considerations when making gun parts with a CNC machine?
Yes, there are legal considerations when making gun parts with a CNC machine. It is important to comply with federal and state laws regarding firearm manufacturing, including obtaining necessary licenses and following regulations for selling or distributing parts.